cases
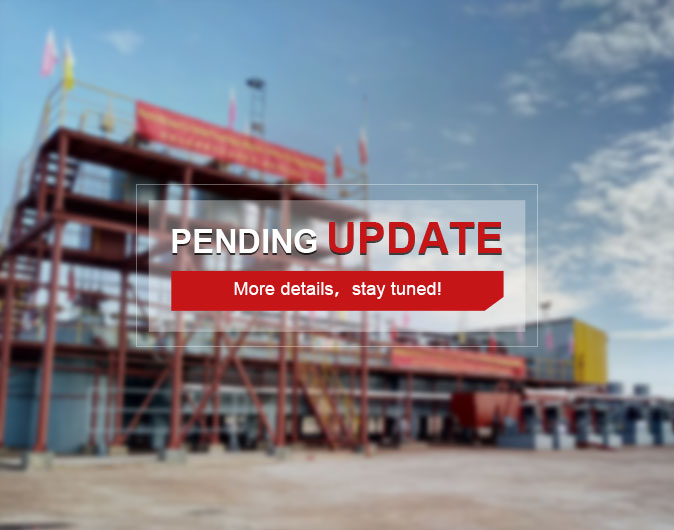
A 200tpd gold CIP plant was originally expanded and put into operation in 1995. This project was reconstructed and expanded on the original basis. The ore belonged to the gold-bearing low sulfide ore. The metal sulfide in the ore mainly included pyrite, and contained a small amount of chalcopyrite, galena, chalcocite, azurite, metal oxide ore and limonite.
Crushing: Two-stage a closed-circuit crushing process was adopted. The raw ore was fed into the belt conveyor by the chute feeder and then transported to one-stage jaw crushing. Then the crushing products were sent to the screening. The oversize product returned to the two-stage cone crushing by the belt conveyor, and then sent to the screening with one-stage crushing products. The qualified undersize was sent to the fine ore bin through the belt.
Grinding: The flotation and grinding adopted one-stage a closed-circuit process. The bottom of the fine ore bin was equipped with the disc feeder, which transported the ore to the ball mill for grinding by the belt. The grinding products were sent to the spiral classifier or cyclone for classifying. The unqualified products returned to the ball mill for regrinding, and the qualified products were sent to the flotation operation.
Separation: The slurry entering the flotation operation was stirred first, and then entered to one-stage roughing, two-stage scavenging and two-stage concentration. The flotation tailings were transported to the tailings pond by two-stage transportation. The flotation concentrate was dehydrated by two-stage thickening and filtration to obtain the gold concentrate, and then the lean solution after size mixing was sent to concentrate cyanidation regrinding. The concentrate regrinding adopted one-stage a closed-circuit process. The grinding products adopted the cyclone for classifying, the unqualified sand setting returned to the ball mill for regrinding, the qualified overflow products were sent to thickener for concentration, and then sent to the cyanide carbon-in-leach process system, where the slurry and activated carbon flew in reverse. After the cyanide leaching, the slurry was sent to the filtration by safety screen, the filtrate returned for use and the filter cake was exported. The gold-bearing carbon of cyanide leaching was sent to desorption electrolysis, and the gold mud was sent to smelting to produce the alloy gold. The lean solution obtained by filtration adopted the acidification to extract the copper. Adding the concentrated sulfuric acid, the copper ions were precipitated to the bottom of the tower by acidification Plated Though Hole (PTH) tower, and then the cuprous thiocyanate was obtained by the filtration. Then, the poor solution was neutralized by adding lime and then returned to the cyanidation system for recycling.
For the flotation system, the gold concentrate grade was 40g/t, the yield was 8.23% and the recovery rate was 94.0%. The copper concentrate grade was 2.1%, the yield was 8.23% and the recovery rate was 81.0%. For the concentrate cyanidation system, the recovery rate of gold was 93.15%, the copper recovery was 16%. The total gold recovery of flotation and cyanidation was 87.56%, and the copper recovery was 13.0%.
To find out more about our products and solutions, please fill out the form below and one of our experts will get back to you shortly.