solutions
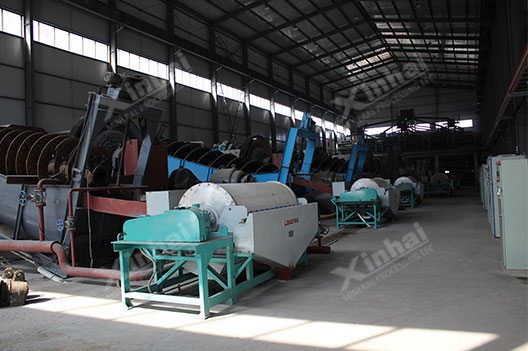
[Introduction]: The hematite processing line adopting stage grinding and stage separation for high separation efficiency. The combination of strong magnetic separation and reverse flotation process ensures the concentrate grade and environmental protection.
[Improvement]: Hematite separation process is suitable for complex structure hematite ore, such as hematite ore and impurities with uneven distribution of particle size, hematite ore with large content of fine particle, hematite ore with small amount of magnetite and the gangue minerals containing quartz or kaolin.
In the first grinding and classification stage, ball mill and hydrocyclone consists the closed circuit. It guarantees the classification efficiency and classification particle size. At the same time, it separates part of regular concentrates at advance. Part of low-grade tailings are discarded by high-gradient magnetic separator. It can reduce the middling regrinding amount and metal loss, also avoiding overgrinding.
The magnetic separation can separate regular coarse concentrates and tailings in time, which fits the principle of early recovery and early discarding as possible. It also reduces the flotation workload and costs.
Strong magnetic separation can recover the fine particle iron ore. It has double effects of desliming and discarding tailings. It can provide good conditions for flotation operation.
Verse flotation has a simple reagent system, which can obviously reduce the flotation reagent into the slurry. It can reduce the adverse reactions of flotation.
To find out more about our products and solutions, please fill out the form below and one of our experts will get back to you shortly.