cases
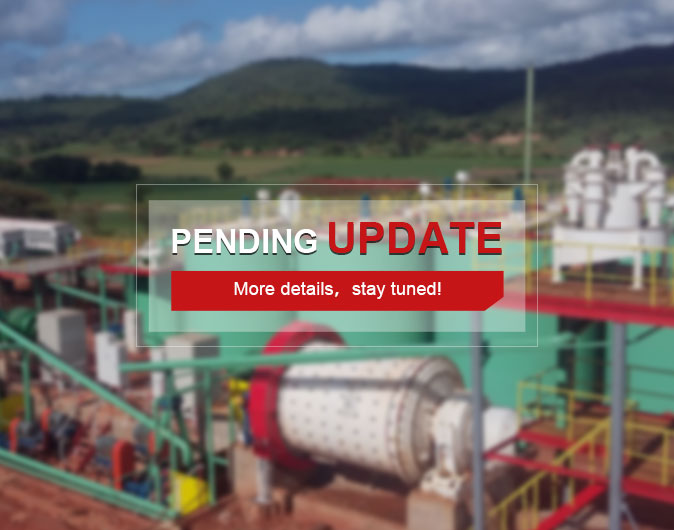
The metal minerals in the ore included pyrite, chalcopyrite, limonite, hematite, etc. Gangue minerals included quartz and calcite. The raw ore contained granular gold. The upper part of the mine was oxidized ore, and the lower part was sulfide ore.
Crushing and screening system: The crushing and screening system adopted two semi-closed circuit process. The ore in the raw ore bin was fed to the jaw crusher by the chute feeder for coarse crushing, and the coarsely crushed products were transported to the double-layer circular vibrating screen by the No.1 belt conveyor for screening. The product on the upper screen was fed to the jaw crusher for crushing, and the crushed product and the product on the lower screen were fed to the No. 2 belt conveyor together, and then fed into the cone crusher by a heavy-duty mobile belt conveyor for fine crushing. Together with the coarsely crushed product, it was returned to the double-layer circular vibrating screen via the No.1 belt conveyor. The particle size of the product under the screen was -12mm and was transported to the powder ore bin by No.3 and No.4 belt conveyor, which formed two semi-closed crushing processes.
Grinding and grading system: It adopted two-stage closed-circuit grinding process. The first stage grinding and grading adopted a grid ball mill and a single spiral classifier, and the grinding fineness was -200 mesh accounting for 45-50%; the second stage grinding adopted an overflow ball mill and hydrocyclone, and the final grinding fineness was -200 mesh accounting for 70%.
Gravity separation system: In combination with the recommended process flow and ore properties of beneficiation test, at the discharge point of first stage ball mill added a gravity separation system. The ore pulp discharged from the first stage of the ball mill was selected by a sawtooth wave jig, and the coarse beneficiation concentrate was selected by a shaker. The concentrate of the shaker was a heavy sand product, which was dewatered for sale after being precipitated in a precipitation tank. The middle tailings of the shaker were pumped into the thickener, and then sold as gold concentrate after being dewatered with gold concentrate in flotation.
Flotation separation system: Flotation adopted a process of one roughing, two scavenging and three concentration processes. The pulp flew to the flotation system by itself after agitation. The roughing and scavenging operations adopted XCF-4 and KYF-14 flotation units. The concentration operation adopted BF-2.8 flotation cell. The pulp entered the next operation in turn, and the flotation foam returned to the previous operation in turn. The flotation concentrate flew to the pump box by itself and was pumped into the concentrate dewatering system by the concentrate pump. Flotation tailings was pumped to the tailings dewatering system.
Concentrate dewatering system: The flotation concentrate was pumped into the central transmission thickener for thickening through the concentrate pump. The thickener overflows returned to the production system. The underflow concentration of the thickener was about 40%, which was pumped into the chamber filter press for filtration, and the filtrate was pumped to the thickener. The filter cake was the final gold concentrate, which was stored in the concentrate pond for sale, thus formed the two-stage mechanical dewatering process.
Tailings dewatering system: Flotation tailings entered the tailings dewatering system. The tailings dewatering system adopted the two-stage mechanical dewatering process of thickening and filter press process. Concentration adopted a central transmission thickener, with 35%-40%-concentration underflow of the thickener, which was pumped into the chamber filter press through a slurry pump. The filter press filtrate and the overflow of the thickener returned to the high seated production pool through the pump. The tailings filter cake was stored in the temporary tailings pond. According to the company's production plan, tailings will be used as raw materials for brick-making in the future.
The raw ore was ground with a fineness of -200 mesh accounted for 70.1%. The gold grade reached 335.4g/t-348.7g/t and the gold recovery rate of heavy sand 1 was 53.51%-56.31% through gravity separation by shake table. Heavy sand 1 contained granular gold with a gold grade of 30.2g/t-43.51g/t, and heavy sand 2 can be obtained with a gold recovery rate of 9.0%-10.41%. The flotation gold ore with a gold grade of 24.26g/t-29.38g/t and recovery rate of 25.85%-29.05% could be obtained from the tailings of gravity separation by flotation. The recovery rate of gold in the beneficiation test of gravity separation and flotation process reached 91.56%-92.57%.
To find out more about our products and solutions, please fill out the form below and one of our experts will get back to you shortly.