cases
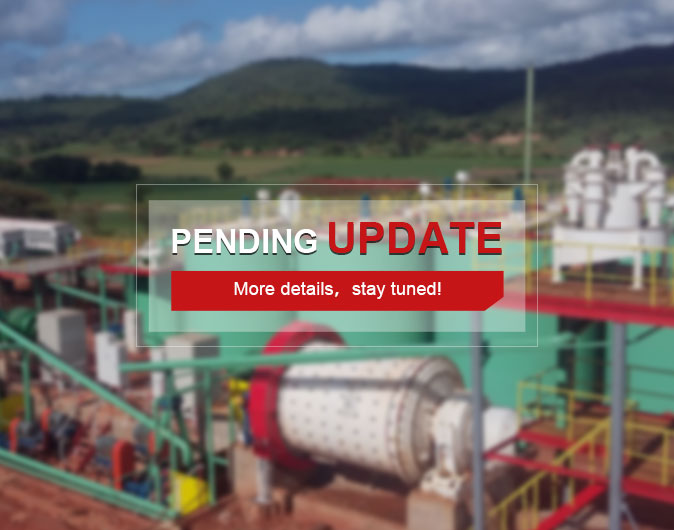
The copper grade was 0.87%, and the maximums size of the raw ore was 350mm. The metal minerals were mainly chalcopyrite, pyrite, tetrahedrite, malachite, etc., and gangue minerals included quartz, calcite, dolomite, chlorite, sericite, tourmaline, etc. Copper was the main object of recycling.
Crushing and screening stage: Two-stage one closed-circuit crushing and screening process was adopted. The raw ore was transported to the raw ore bin of the processing plant, and then it was fed to the jaw crusher by a plate feeder for coarse crushing, and the coarsely crushed product was transported by a belt conveyor to a auto-centering vibrating screen for screening. The screen mesh was 12mm. The larger materials on the screen were transported by the belt conveyor to the cone crusher for fine crushing, and the finely crushed products and the coarsely crushed products were sent to the circular vibrating screen by the belt conveyor to be sieved again. The fine materials under the screen were transported to the powder ore bin by the belt conveyor;
Grinding and beneficiation stage: a closed-circuit grinding and classifing process was adopted, and the belt conveyor was used to return coarse particles.
Copper was extracted by one roughing, three scavenging and three concentration flotation process; sulfur was extracted by one roughing, two scavenging and three concentration flotation process.
There was a belt feeder at the bottom of the fine ore bin. The belt feeder fed the fine ore to a wet grid ball mill for grinding. The discharge end of the ball mill was equipped with a cylindrical screen. After screening, the coarse particles were transported by belt conveyor back to ball mill for regrind; the slurry under the screen was pumped into the XCII Xinhai wear-resistant cyclone for classification, and the underflow of the cyclone returned to the ball mill for regrind, forming a closed-circuit grinding process. Grinding fineness reached 75% of -200 mesh.
The overflow of the cyclone flowed into the high-efficiency agitation tank for adding reagent and mixing, and then entered the copper flotation process of one roughing, three scavenging and three concentration.
SF-4 flotation machine was used for rough flotation and three scavenging separation process, and SF-2.8 flotation machine was used for three concentration process, and the middle ore was returned in turn; the flotation tailings were lifted from the lifting agitation tank to the efficient agitation tank for adding chemical and mixing, then entered the sulfur flotation process of one roughing, two scavenging and three concentration. SF-4 flotation machine was used for flotation tailings roughing and two scavenging separations, and SF-4 flotation machine was used for concentration Ⅰprocess, SF-2.8 flotation machine for concentration Ⅱ and concentration Ⅲ process, and the middle ore returned in turn;
Concentrate dehydration stage: both of the dehydration of copper and Sulphur concentrate adopted a two-stage dehydration process of concentration and filtration. Concentrate thickening adopted efficient improved thickener, and filtering adopted ceramic filter. The water content of the final concentrate was less than 20%;
Tailings dewatering stage: the tailings adopted a cyclone-dewatering screen-thickener-filter press mechanical dewatering process. The flotation tailings were pumped by a rubber pump into a concentration cyclone for classification. The underflow flowed to the dewatering screen for dewatering. The overflow first entered the high-efficiency reformed thickener for concentration, and then was pumped into the filter press for filtration. The product on the dewatering screen and the filter cake of the filter press were combined and discharged for dry storage.
The final product of the project was copper concentrate. The copper concentrate grade was 23.00%, the copper concentrate production rate was 3.45%, and the copper recovery rate was 91.21%. It can provide the society with 10,350 tons of copper concentrate every year, and had strong profitability.
To find out more about our products and solutions, please fill out the form below and one of our experts will get back to you shortly.