cases
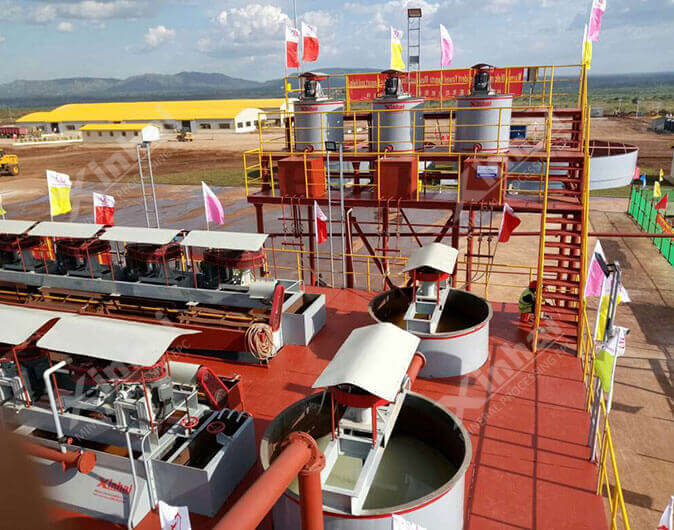
The ore consisted of iron, phosphorus and other metallic elements as well as loose igneous carbonatite weathering residue and hypergenesis-based crandallite and argillaceous hematite clay. The existence of huge slime caused difficulty in the separation and purification of apatite and magnetite. All minerals were inter-wrapped and associated so that liberalization was difficult. The isomorphism was dominant as titanium, iron, manganese, aluminum and magnesium lattices replaced each other. As a result, the ore composition was much complicated.
Desliming: raw materials were fed by loader to the raw ore bin under which belt conveyor and belt feeder were installed. The materials were transported to the agitation tank and mixed with water. The slurry was pumped by slurry pump to the desliming cyclone where slime was transported to the tailings settling pond and underflow flowed by gravity to the ball mill.
Grinding: one-stage closed-circuit grinding process comprising ball mill, pump and classification cyclone. Cyclone overflow flowed by gravity to the high-efficiency agitation tank, mixed with the reagent and then entered the flotation process.
Flotation: direct flotation process of one-stage roughing, one-stage scavenging and two-stage concentration. Flotation concentrates were pumped by froth pump to the concentrates pump box.
Concentrates and tailings dewatering: concentrates were pumped to the concentrates dewatering system, where phosphorus concentrates were gained. Flotation tailings were pumped to the tailings dewatering system. Dry tailings were transported by dump trucks to the tailings pond, and filtrate returned for recycling.
The project adopted advanced and well-developed Chinese equipment and process so that long-term safe, stable and continuous operation was ensured and qualified products were produced. While meeting the process needs, Xinhai managed to protect the environment both at source and at the end. As a result, the costs were cut, construction duration shortened and investment return accelerated.
To find out more about our products and solutions, please fill out the form below and one of our experts will get back to you shortly.