cases
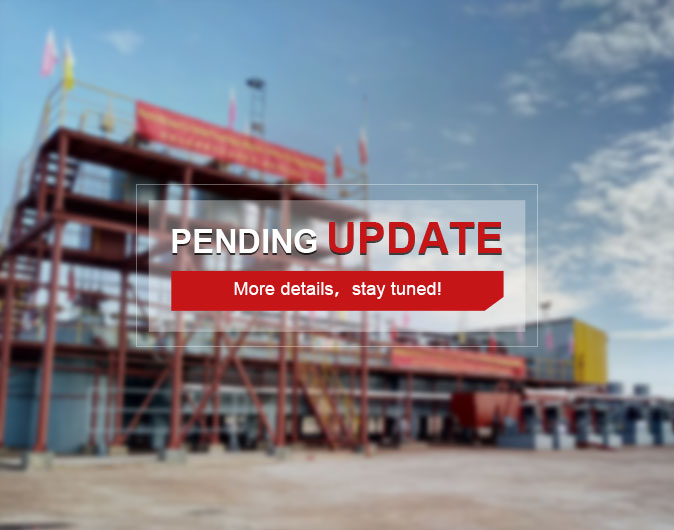
The phosphate ore of this project was a kind of glufosite ore which was hard to be separated, had complex properties and high impurity content. In particular, the vitrinite, containing more than 3% impurities, belonged to the carbonaceous magnesium (calcium) silica phosphate ore, which made the mineral separation more difficult.
The stage of crushing and screening: Used the process of two-stage and one closed-circuit crushing and screening. The raw ore was stored in ore yard, and loaded with a forklift truck. An electromagnetic vibrating feeder was installed at the bottom of the primarybin, and a jaw crusher was used for coarse crushing. After coarse crushing, the materials were transported to the self-centered vibrating screen by the 1# and 2# belt conveyor for screening. The materials on the screen (+12mm) were transported to the fine jaw crusher by the 3# belt conveyor for fine crushing. The finely crushed and the coarsely crushed products were transported back to the vibrating screen by the 2# belt conveyor together to form a closed-circuit crushing. The materials under the screen (-12mm) were the qualified in the crushing stage and were directly put into the powder ore bin.
The stage of grinding and grading: Used the process of two-stage closed-circuit grinding + decarbonization flotation + one-roughing, one-scavenging, one-concentration positive flotation + one-roughing, two-scavenging reverse flotation + one-roughing, one-scavenging, one-concentration sulfur flotation. A pendulum feeder, installed at the bottom of the powder ore bin, sent materials to the grid ball mill by 4#、5# belt conveyor for coarse grinding. There was a cylindrical screen at the discharge end of the ball mill, and the large particles on the screen were transported by 6 #, 7 # belt conveyor back to the ball mill for regrinding. The pulp under screen was pumped into a hydrocyclone for grading, and the underflow was back to the ball mill for regrinding, forming the process of first stage closed-circuit grinding.
The overflow from the hydrocyclone flowed into a pump box, and was pumped into the hydrocyclone group for grading. The underflow flowed into a overflow ball mill for fine grinding. Products flowed into the previous pump box for grading, forming the second stage closed-circuit grinding. The grinding fineness is 200 mesh, accounting for 85%.
The overflow of the hydrocyclone group flowed into the ordinary agitation tank with reagents and size mixing, then flowed into XCF/KYF-4 air-charging flotation cell for decarbonization flotation. The flotation froth was dehydrated in the settling pond to obtain carbon-containing tailings. The overflow of the settling pond could be returned to the second stage closed-circuit grinding.
After decarburization flotation, the pulp was lifted from the lifting agitation tank to a ordinary agitation tank with reagents and size mixing, then flowed into XCF/KYF-4 air-charging flotation cell group for heating and positive roughing flotation. The roughing froth products flowed into the XCF/KYF-4 air-charging flotation cell group for positive concentration flotation, and then the concentrated concentrates entered into reverse flotation. The pulp in the roughing tank flowed into the XCF/KYF-4 air-charging flotation cell group for positive scavenging flotation, and then the scavenged concentrate and concentrated tailings flowed into the high-efficiency modified thickener for dehydration. The underflow was pumped into the positive roughing flotation, and the overflow could be returned to system for recycle. The concentrates of positive concentration flotation was lifted from the lifting agitation tank to a ordinary agitation tank with reagents and size mixing, then flowed into XCF/KYF-4 air-charging flotation cell group for reverse roughing flotation. Froth products were the tailings. The pulp in the roughing tank flowed to twice scavenging operations. Froth products of scavenging I and II were returned to previous operation in sequence. The pulp in scavenging II tank was the final phosphate concentrate.
The positive scavenging flotation tailings entered to the lifting agitation tank with reagents and size mixing, then flowed into XCF/KYF-4 air-charging flotation cell group for sulfur roughing flotation. The roughing froth products flowed into the XCF/KYF-4 air-charging flotation cell group for sulfur concentration flotation, and the concentrated froth products were sulfur concentrates. The pulp in the sulfur roughing flotation tank flowed into XCF/KYF-4 air-charging flotation cell group for sulfur scavenging flotation. The scavenging concentrates and concentrating tailings were returned to sulfur roughing flotation operation. The scavenging tailings and reverse roughing flotation froth products were all the final tailings, entering to tailings dehydration stage.
The stage of concentrate dehydration: It used the settling pond to dehydrate for flotation sulfur concentrate. The overflow from settling pond could be returned to the stage of sulfur flotation for recycle. The flotation phosphate concentrate used the the mechanical method of thickener + filter to dehydrate. The phosphate concentrate used a high-efficiency modified thickener to thicken and disc type vacuum filter to filter. The filter cake was the final concentrate with a water content of less than 12%. The filtrate was returned to the thickener, and the overflow from the thickener could be returned to the stage of reverse flotation for recycle.
The stage of tailings dehydration: Flotation tailings used the mechanical method of thickener + filter to dehydrate. It used high-efficiency modified thickener to thicken and disc type vacuum filter to filter. The filter cake was the final concentrate with a water content of less than 12%. The filtrate was returned to the thickener, and the overflow from the thickener could be returned to the grinding stage for recycle.
The final products were sulfur concentrate and phosphate concentrate. When reaching the design scale, the annual output of phosphate concentrate was 96,512 tons, with a grade of 30%; sulfur concentrate was 0.8571 million tons, with a grade of 35%.
To find out more about our products and solutions, please fill out the form below and one of our experts will get back to you shortly.