cases
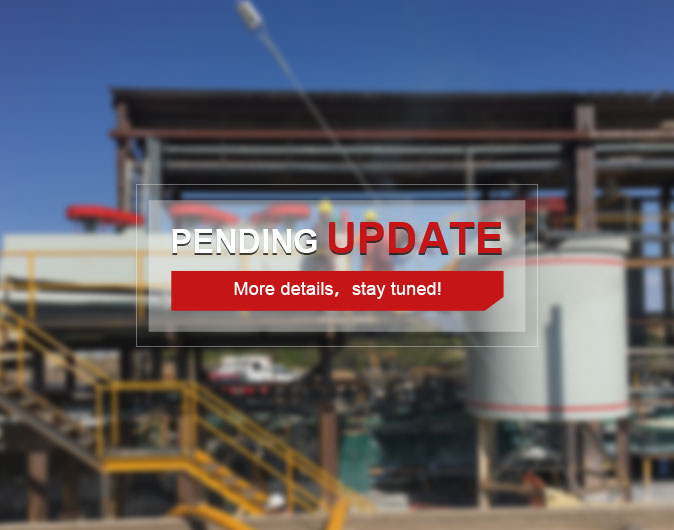
The raw ore contained 1.03 g/t Au and 1.43 g/t Ag, with low contents of other elements such as Cu, Pb, Zn and S. Gold was the only valuable element available for recovery in this ore. The types of raw ore metal minerals were relatively rich, mainly including hematite, magnetite, limonite and a small amount of pyrite, galena, sphalerite, chalcopyrite, etc.; non-metallic minerals are mainly quartz, long Stone, mica, calcite, etc.
Sollution 1: After the raw ore ground, the gold wasrecovered by the gravity separation-leaching process. The raw ore (-2mm) was groundto 85% of -200 mesh. After gravity separation, the concentrate was obtainedwith the yield rate of 0.207%, the gold grade of 228g/t, the gold recovery rateof 45.79%, and the gravity separation tailings contained 0.56 g/t gold; thegravity separation tailings enter the leaching operation; the gold leachingrate was 87.50% (relative to the raw ore 47.43%) when the leaching agent was Holy,and the total recovery rate of gravity separation-leaching gold was 93.22%. Whenthe leaching agent was sodium cyanide, the gold leaching rate was 89.29%(relative to the raw ore 48.40%), and the total recovery rate ofgravity-leaching gold was 94.19%.
Sollution 2: After the raw ore was separated by gravityand gravity separation tailings was classified, the coarse-grained product(sand) adopted the heap leaching process to recover the gold; the fine-grainedproduct (mud) adopted the heap leaching process to recover the gold. The raw oreused in this scheme was heap leaching sample. The raw ore was stirred forpulping, classified by 16 meshes, and the product under the screen wassubjected to 3 gravity operations (jigging, shaking table, elutriation) obtaina panning concentrate with a yield of 0.002%, a gold grade of 4161g/t, and agold recovery rate of 8.876%; the jigging tailings were deslimed to obtain themud product, which was fed into the leaching operation. When the leaching reagentwas Holy, the operating leaching rate of gold was 84.44%, and the relative leachingrate of raw ore was 22.58%; when the leaching reagent was sodium cyanide, theoperating leaching rate of gold was 88.89%, and the relative leaching rate ofraw ore was 23.77%. The coarse-grained product from the jigging tailings wasmixed with the shaker tailings and the 16 mesh sieve product to form the sandproduct. Sand products entered the heap leaching operation. When the leaching reagentwas Holy, the operating leaching rate of gold was 85.03%, and the relative leachingrate of raw ore was 53.01%; when the leaching agent was sodium cyanide, theoperating leaching rate of gold was 86.83% and the relative leaching rate ofraw ore was 54.13%. When the leaching reagent was Holy, the total gold recoveryfrom gravity separation- heap leaching-leaching gold was 84.47%; when theleaching reagent was sodium cyanide, the total gold recovery from gravityseparation-heap leaching-leaching gold was 86.78%.
Sollution 3: After being ground, the raw ore adopted theprocess of gravity separation-chlorination leaching to recover gold. Solution 3exploration test used test 4.2 to obtain gravity separation tailings, withslurry concentration of 20%, sodium chloride dosage of 50 g/l, sodiumhypochlorite dosage of 10 g/l, normal temperature leaching time of 4h, goldleaching rate is 51.78% (compared with raw ore 28.07%), and the leaching rateis relatively low. The total recovery of gold from gravity separation-chlorinationleaching of the raw ore was 73.86%.
To find out more about our products and solutions, please fill out the form below and one of our experts will get back to you shortly.