cases
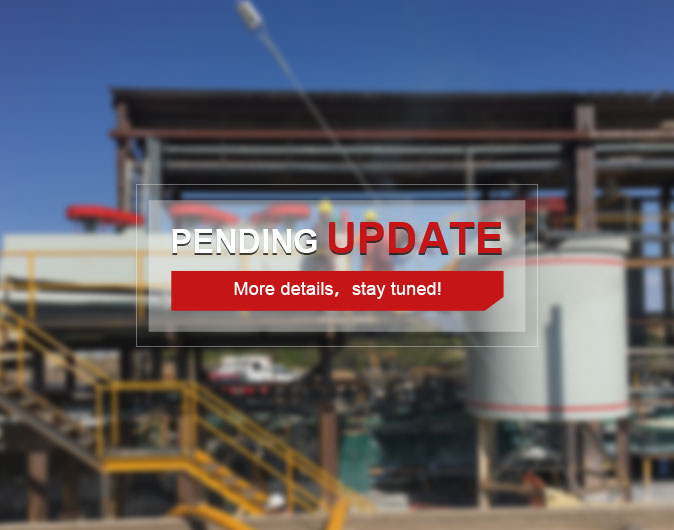
The raw ore was characterized by simple composition. The metallic minerals were mainly natural gold. There were more pyrite and limonite, a small amount of magnetite, and others. The gangue minerals included mainly neutral plagioclase, horn amphibole, and hypomphibole, followed by quartz, chlorite, calcite, and sericite, and a small amount of albite.
Crushing and screening: raw materials were transported from the mining site to the raw ore bin by trucks and forklifts and stacked in the dump. Then it was fed by chute feeder to the jaw crusher for coarse crushing. The coarse crushing products were transported to the auto-centering vibrating screen by the belt conveyor for screening. Oversized products were transported to the hydraulic cone crusher for fine crushing by the belt conveyor. The fine products were sent to the auto-center vibrating screen for re-screening by the belt conveyor to form the closed circuit.Undersized products were sent to the fine ore bin by belt conveyor to gain a product size of -15mm.
Grinding and classification: fine ore was fed evenly by electric vibration and belt conveyor to the roller-bearing grid ball mill for coarse grinding. Ground materials were fed to the spiral classifier, where settled materials returned to the ball mill, and overflow flowed by gravity to the second-stage grinding pump. The slurry was pumped to the hydrocyclone, where settled materials returned to the roller-bearing grid ball mill, and regrind products flowed by gravity to the second-stage grinding pump to form the closed circuit. The overflow flowed by gravity to the liner screen to remove wood chips and other impurities, and undersized slurry flowed by gravity to the high-efficiency transformed thickener.
Concentration: Grinding products thickened to 40% were leached and carbon adsorption in the double-impeller high-efficiency leaching tank, where added NaCN and lime, and feed air by Roots blower. Au reacted with NaCN under the alkaline environment to produce the gold-cyanide complexion and was absorbed by active carbon. The saturated gold-bearing carbon was reversely taken out of the No.3 leaching tank and fed to the carbon screen. Undersized slurry returned to the No.1 leaching tank, and the gold-bearing carbon was conveyed to the carbon stage tank of the desorption electrolysis system. After regular treatment, the gold slime was produced for sales.
Tailings dewatering: Tailings dry stacking was adopted, with a final tailings water content of less than 20%. Dry tailings were stacked on-site, and filtrate returned for recycling. In practical production, cyanide and other harmful ions in the backwater neutralized by adding bleaching powder to avoid affecting production indicators.
The project had a leaching rate of 95.26%, a desorption rate of 96.00%, and a recovery rate of 91.45%.
To find out more about our products and solutions, please fill out the form below and one of our experts will get back to you shortly.