cases
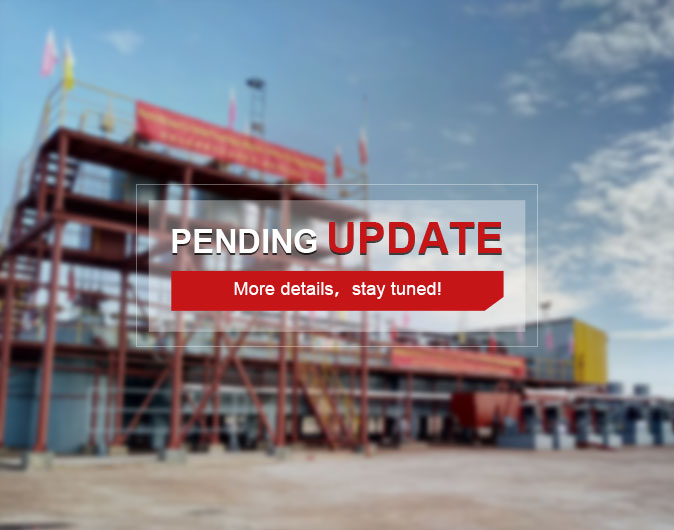
80% from La Julia,the copper sulphide was 3%/ton, the gold was 4grs/ton; 20% from La Compañía, the copper was 0.80%, the silver was 220grs/ton, the gold was 4.5 hrs/ton.
Crushing and screening system: The crushing screening system was adopted two stage one circuit flow. The raw ore was deposited in the raw ore yard, and the ore was loaded by forklift truck. Feed the ore to the raw ore bin, a chute feeder was provided for the bottom of the bin. Feed into the jaw crusher for coarse crushing. After crushing the material was transported by belt conveyor to circular vibrating screen for screening, the larger grains upper the sieve were transported to the finely jaw crusher for fine crushing, finely discharge ore by the belt conveyor transport to the circular vibrating screen for screening, made up crushing screening closed-circuit. Lower sieve -20mm material was transported to fine ore bin via belt conveyor.
Grinding and separation system: Grinding and classification system adopted a closed-circuit grinding classification flow. Swaying feeder was provided at the bottom of the fine ore bin, feed to the energy-saving grid ball mill by the belt conveyor for grinding. Discharge of the ball mill transported by the slurry pump to the hydrocyclone for classifying. Hydrocyclone bottom flow returned to the ball mill for regrinding, overflow into floatation system. The flotation system adopted one roughing two scavenging and two cleaning process flow, got the flotation concentrate. Flotation concentrate entered the concentrate dewatering system, tailings into tailings dewatering system.
Concentrate dewatering system: The flotation concentrate was transported to the thickener by slurry pump for concentration, and the bottom flow of the thickener entered the agitation tank for buffering, and then was transported by slurry pump to the chamber filter press for pressure filtration and dewatering. The filtrate was recycled return to the system, and the filter cake was transported to the concentrate storage by forklift.
Tailings dewatering system: The flotation tailings were transported to the thickener by slurry pump. Adding flocculant accelerates sedimentation, the underflow of the thickener entered the agitation tank for buffering. Then sent to the filter press for dewatering by the slurry pump, the filtrate was recycled return to the system, and the filter cake was transported to the concentrate storage by forklift.
The copper concentrate grade was 20% and the recovery rate was 90%, the concentrate yield was about 13.5%.
To find out more about our products and solutions, please fill out the form below and one of our experts will get back to you shortly.