cases
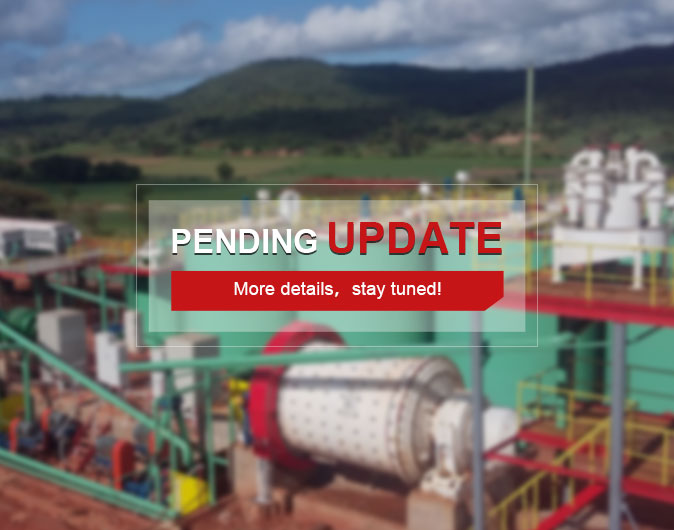
The ores were primary ores, which were roughly divided into brass, pyrite, magnetite, tremolite skarn according to the mineral assemblage, structure and structural characteristics. The main useful elements in the ore were copper, iron, etc., the industrial type of ore was copper iron ore.
Crushing and screening: After the raw ore was extracted from the mine, it was crushed to 0-150mm by a jaw crusher set at the pit mouth, then transported to the raw ore storage yard by car. The raw ore in the storage yard was pushed to the raw ore gathering bin under which the chute feeder was installed. The raw ore was uniformly delivered to the belt conveyor, then transported to the circular vibrating screen for screening. The oversize materials returned to the hydraulic cone crusher for fine crushing through the belt conveyor. The fine products were also transported to circular vibrating screen for screening, forming a closed circuit crushing and screening process. The undersize material was transported to the powder ore for storage through the belt conveyor, and the particle size of the crushed product was -12mm.
Grinding & classification + instant flotation: The powder ore was fed to belt conveyor by motor vibration feeder, and evenly sent to the grid ball mill by belt conveyor, the coarse grinding products were sent to the spiral classifier, the classifier sand returned to the ball mill, the overflow flew into the instant flotation. The tailings of instant flotation operation adopted Xinhai wear-resisting rubber pump to pump them into the Xinhai wear-resisting hydrocyclone for second classification, the cyclone settling returned back to the ball mill for regrinding, and the cyclone overflow flew to the copper flotation.
Copper flotation: In addition to the above copper instant flotation, the instant flotation tailings were sent to second classifying by a cyclone, and the cyclone overflow flew to the copper flotation operation. The copper flotation adopted one roughing, three scavenging and four concentrating to recover the fine copper mineral, and adopted one concentrating and one scavenging to recover the sulfur. Magnetic separation of magnetite: The copper flotation tailings were sent to the semi-counter-current magnetic separator by Xinhai wear-resisting rubber pump for two stage magnetic separation, and then produced the iron concentrate.
Dewatering of copper concentrate: The copper flotation concentrate and instant flotation concentrate were pumped together to the efficient improved thickener for concentration. The concentrated slurry was sent to the filter press by Xinhai wear-resisting two-stage pump for filtration, and the filtered concentrate was transported to the warehouse by the forklift truck. Dewatering of iron concentrate: The iron concentrate was pumped to the concentrator by Xinhai wear-resisting rubber pump, and the concentrated pulp flew to the disk-type vacuum filter. The filtering products were transported to the iron concentrate warehouse for storage by the belt conveyor. Sulfur concentrate disposal: Due to the different nature of the raw ore, the sulfur concentrates rate and grade fluctuated greatly. There was no special mechanical dewatering equipment for sulfur concentrate, the sulfur concentrate flew to the sedimentation tank for natural dewatering. Tailings disposal: The tailings flew directly into the tailings pond.
Finally, the copper concentrate rate was 6.40%, the sulfur concentrate rate was 5.90%, and the iron concentrate rate was 54.36%.
To find out more about our products and solutions, please fill out the form below and one of our experts will get back to you shortly.