cases
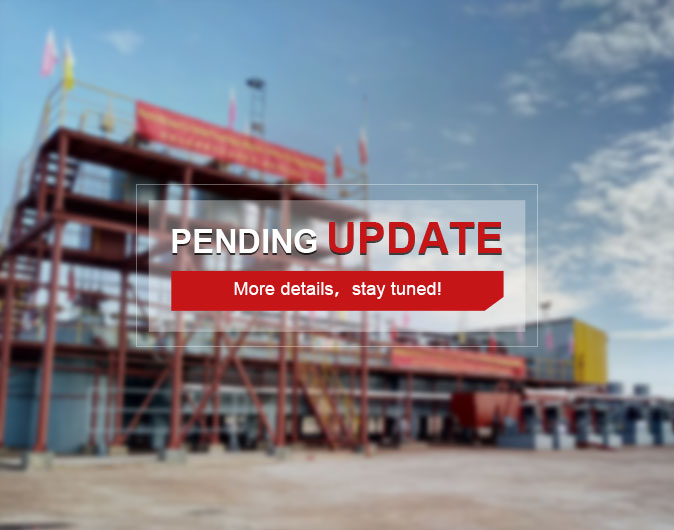
The Gansu 500tpd gold mineral processing plant was an EPCM+O project. Xinhai worked to achieve high recovery of gold and other valuable minerals by cutting costs and maximizing benefits and attaching great importance to workers’ safety, environmental protection and energy conservation.
Crushing and screening: Two-stage a closed circuit crushing and screening was adopted. The bottom of raw ore bin is equipped with the plate feeder. The jaw crusher was used in the coarse crushing. The coarse crushing products were transported to the circular vibrating screen through 1# belt conveyer. The oversize products (+12mm) were transported to cone crusher for fine crushing by 2# belt conveyer. The fine crushing products and coarse crushing products returned to the vibrating screen. The undersize material (-12mm) was the qualified material in the crushing stage, which was transported to the fine ore bin by 3 and 4# belt conveyor.
Grinding and separation: One-stage grinding and classifying was adopted. After the one-stage roughing, the roughing middlings were sent to the second roughing after the regrinding and reclassifying. The second roughing concentrate was sent to the concentration with the first coarse roughing concentrate, and the second roughing tailings were sent to the scavenging (three times of concentration and two times of scavenging). The bottom of the fine ore bin was equipped with the electric vibration feeder, which fed the ore into the 5# belt conveyor to be transported to the cylinder ball mill for rough grinding. The discharge of ball mill was pumped into the hydraulic cyclone, and the underflow returned to the ball mill for regrinding, forming one-stage closed-circuit grinding process. The grinding fineness of -200 mesh accounted for 65%. The overflow flew to the high efficiency agitation tank first, and then flew to the 8 m3 air inflation flotation machine for roughing I after dosing and mixing, the pulp in the tank was the tailings, which flew to a pump box, and then was pumped into the hydrocyclone unit for second-stage classifying. The underflow flew to the overflow ball mill for grinding, the discharge of ball mill returned to the above pump box, and then returned to the second-stage classifying with roughing I tailings, forming the second stage closed-circuit grinding. The grinding fineness of - 200 mesh accounted for 85%. The overflow of cyclone unit flew to the high efficiency agitation tank, and then flew to the 8 m3 air inflation flotation cell for roughing II after dosing and mixing, the foam products of roughing II and foam products of roughing I flew together to 4 m3 air inflation flotation cell for three stage concentration (3/2/1). The flotation gold concentrate was obtained after three stage concentration, the products in the concentration I, II, III returned the previous operation. The products in the roughing II flew to the two times of scavenging. The flotation cell used in two times of scavenging was 8m3 air inflation flotation cell. The foam products of scavenging I , II returned to the previous operation in turn, and the tailings of scavenging II were the final flotation tailings.
Concentrate dewatering: The flotation gold concentrate adopted thickener and press filter to dewater. The gold concentrate was concentrated by the efficient improved thickener and the press filter. The filter cake was the final concentrate with water content less than 20%, and was transported to the concentrate warehouse for stockpiling by the belt conveyor. Both filtrate and thickener overflow flew to the back pool and then returned to the system for recycling.
Tailings dewatering: The flotation tailings adopted dewatering cyclone + dewatering screen + thickener + press filter. The tailings pulp was pumped into the dewatering cyclone, and the underflow of cyclone flew to the dewatering screen. The overflow entered to the thickener, and the underflow of thickener was pumped into the press filter by slurry pump for pressure filtration. The filter cake was the final tailings with water content less than 20% and were transported to the tailings storage site by belt conveyor for stockpiling. The undersize water returned to the thickener. Both filtrate and thickener overflow flew to the back pool and then returned to the system for recycling.
To find out more about our products and solutions, please fill out the form below and one of our experts will get back to you shortly.