cases
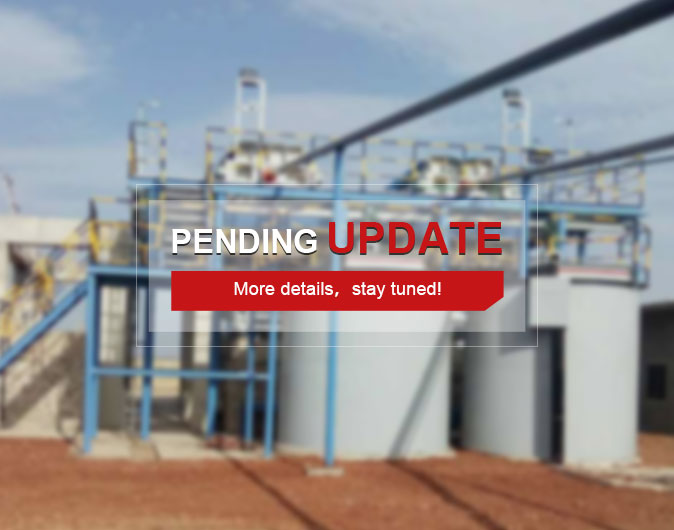
The composition of the ore was relatively simple. Metal minerals were mainly metal sulfides and a small amount of metal oxides. Metal sulfides were mainly pyrite and contain trace galena, sphalerite, etc.; metal oxides were a small amount of hematite, magnetite, etc. Non-metallic minerals were quartz, sericite, muscovite, potash feldspar, calcite, plagioclase and other ores. The main useful element was gold. The type of ore industry was determined to be gold ore.
Three stage and one closed-circuit crushing and screening--heap leaching--carbon adsorption--gold extraction process
Crushing and screening stage: According to the raw ore processing capacity , the maximum size of the raw ore, the final product crushing size and the nature of the ore and other factors, the three-stage and one closed-circuit process was adopted, that was coarse crushing+medium crushing+fine crushing+preliminary screening and checking screening.
Heap leaching process: it adopted multi-layer method of pile building and spray leaching process, the pregnant solution of heap leaching flowed to the pregnant solution pool, and the intermediate liquid of heap leaching returned to the mine pile for cyclic spraying.
Carbon adsorption and gold extraction process: the pregnant solution was extracted using the carbon adsorption, desorption electrolysis and smelting gold extraction process. The carbon adsorption lean solution returned to the heap leaching yard for cyclic spraying, the desorption lean solution returned to the carbon adsorption operation, and the electrowinning lean solution returned to the desorption operation. In the end, we smelted to get the final product-crude gold.
The gold grade of the raw ore of the project was 1.16g/t, the heap leaching rate was 64%, the adsorption rate was 98.5%, the desorption electrowinning recovery rate was 99.5%, the smelting recovery rate was 99.5%, and the comprehensive recovery rate was 62.4%.
To find out more about our products and solutions, please fill out the form below and one of our experts will get back to you shortly.