cases
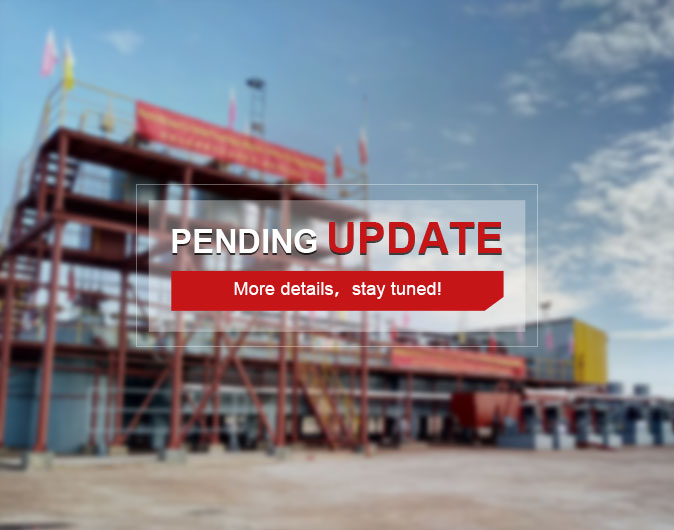
According to the composition of raw minerals, Xinhai learned that the main minerals of the project ore were feldspar and quartz, a small amount of muscovite and tourmaline minerals. The key to obtaining qualified feldspar concentrate and quartz concentrate was the separation of quartz and feldspar.
Two-stage semi-closed-circuit crushing and screening process---One stage closed-circuit grinding and classifying process---One roughing three concentration three sweeping flotation process---Concentrate tailings conveying process
Crushing and screening stage: It adopted two-stage and semi-closed circuit crushing and screening process, which not only significantly reduced energy consumption and saved investment, but also created conditions for the selection of reasonable models, cavity types and feeder input sizes for the third crushing stage. The crushing and screening operations were arranged in separate plants, which greatly saved plant investment. The final product size of crushed ore was -14.4mm; Grinding and classifying stage: The wet grid ball mill used drum feeder to replace the large spoon head, which greatly reduced the impact of the ball mill on the power grid; the spiral classifier added a sand return lifting device at the sand return end to adapt to the drum feeder. The final grinding product had a fineness of 200 mesh accounting for about 67%;
Flotation stage: the flotation equipment adopted SF flotation cells of two specifications, which realized horizontal configuration, and the layout of the entire plant and equipment configuration were economical, compact and reasonable;
Concentrate tailings conveying stage: feldspar concentrate and quartz concentrate flew to their respective thickeners, feldspar concentrate was packaged into the warehouse after three-stage dewatering operations of concentration, filtration and drying, and quartz concentrate was piled up after two stage dewatering operation in thickener and precipitation pool; the tailings flew directly into the tailings pond outside the plant through the tailings collecting pipe.
The feldspar concentrate contained 14.16% K2O+Na2O, and the final yield was 54%; the quartz concentrate contained SiO2 ≥97.87%, and the final yield was 10%; the K2O+Na2O concentrate reached an annual output of 81,000 tons. The amount of SiO2 concentrate reached 15,000 tons per year.
To find out more about our products and solutions, please fill out the form below and one of our experts will get back to you shortly.