cases
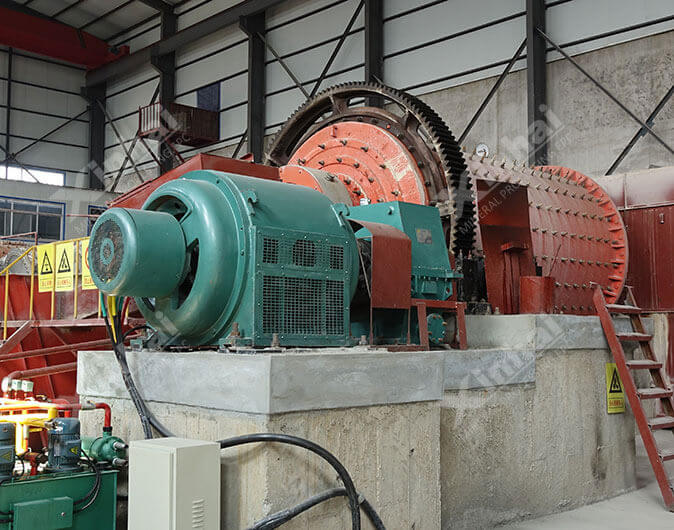
Major minerals were potassium feldspar and albite, which accounted for 60-80%. In white-flesh pink color, potassium feldspar occurred in the form of subhedral plate. Some crystals had cross-hatched twinning. The secondary mineral was quartz accounting for 10-30%, which was in milk white color and occurred in irregular and wormlike form. There was a minor amount of black mica, which occurred in the form of black flake and accounted for 1-5%. White mica occurred in the form of white flake and accounted for 1-5%. Magnetite and tourmaline occurred locally in black plate form.
Crushing and screening: materials were fed by belt conveyor to the jaw crusher for coarse crushing; crushed materials were transported by belt conveyor to the circular vibrating screen for wet screening; oversize materials returned to the hydraulic cone crusher for fine crushing; crushed materials were sent to the circular vibrating screen for wet screening to form closed-circuit crushing. Oversize materials were sent to the fine ore bin to gain a product size of -15mm.
Grinding and classification: fine ore was fed evenly by belt conveyor to the roller-bearing grid ball mill for coarse grinding; ground materials were fed to the spiral classifier, where settled materials returned to the ball mill and overflow flowedby gravity to the separation process.
Separation: medium-field magnetic separation-desliming-indirect flotation. Ground materials flowedby gravity to the magnetic separator to remove impurities; magnetic tailings flowedby gravity to the slurry pump box and were pumped to the desliming hopper; underflow flowedby gravity to the agitation tank and mixed with reagent; the mixture flowedby gravity to the indirect flotation process comprising XCF and KYF flotation cells to remove ferric oxide and mica.
Concentrates dewatering: feldspar concentrates entered the cyclone for classification; overflow was thickened and dewatered in the desliming hopper, while underflow was mixed with materials from the hopper to constitute high-concentration slurry (over 50%) and flow by gravity to the dewatering screen. The water content of final feldspar concentrates was kept below 15%, and they were transported by belt conveyor to the concentrates dump for sales. Water under screen flowedby gravity to the pump box and was pumped to the cyclone for further classification and dewatering.
The plant was able to produce 87,972 tons of feldspar concentrates every year, which had a yield of 73.31%. At the same time, new jobs were created for local residents. As a result, both economic and social benefits were achieved.
To find out more about our products and solutions, please fill out the form below and one of our experts will get back to you shortly.