cases
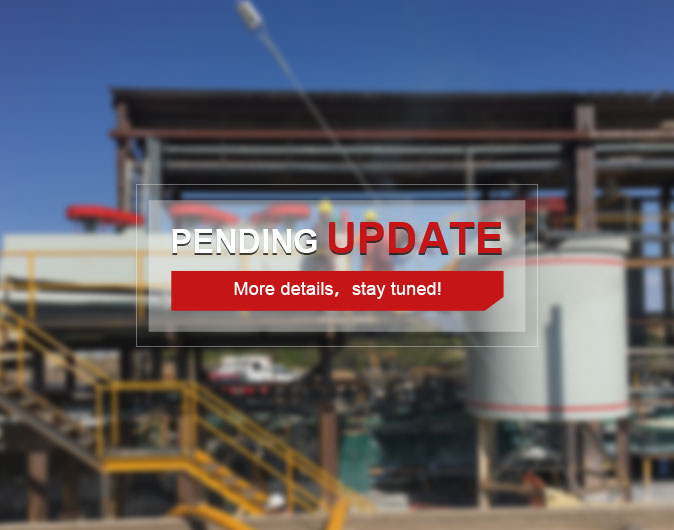
The silica ore was off white in color, with quartz as its main mineral and Fe2 O3 rust film along the ore cracks. Quartz ore texture was fine - grained, the ore structure was a massive structure, and the ore type was vein quartz.
One-stage open-circuit self-grinding + one-stage closed-circuit grinding and classification+ two-stage magnetic separation + one-stage desliming + four-stage scrubbing-desliming + one-stage closed-circuit regrinding.
The raw quartz ore crushed to ≤200mm in the stope was transferred to the raw ore stock dump of the processing plant. The loader shoveled the raw ore into the raw ore bin, then the raw ore was fed to the belt conveyor by the chute feeder and transported to the autogenous mill for grinding. The ore discharged from the mill was screened by a linear vibrating screen. Undersize product was pumped by a wear-resistant rubber pump to the hydraulic classifier for classification. Oversize product on the screen and the underflow product of the hydraulic classifier were returned to the overflow ball mill for regrinding. The discharge of the ball mill flowed to the linear screen through the chute to form a closed-circuit grinding. At the same time, the chute was equipped with an electromagnetic iron remover to remove mechanical iron.
The overflow product of the hydraulic classifier flowed to the medium intensity forward flow magnetic separator for iron removal, while the non-magnetic product flowed to high intensity magnetic separator to further remove iron, so that the iron slurry flowed to the pit of the submerged slurry pump and then was pumped to the sedimentation tank by submerged slurry pump. For the non-magnetic product separated by the high intensity magnetic separator, it flowed to the pump pit, and were pumped by the rubber pump to the hydraulic classifier for desliming.
The underflow of the hydraulic classifier flowed into the high efficiency agitator washer for scrubbing firstly. After scrubbing, the slurry was pumped to the wear-resistant cyclone for desliming and classification, and the cyclone underflow flowed to the agitator scrubber for scrubbing again. After repeating the above process four times, the classification overflow was collected into the pump pit and then pumped to the thickener. The underflow from the last cyclone desliming process flows into the long cylindrical ball mill for fine grinding, and the final grinding fineness was -325 mesh accounting for 95%. The mill discharge was pumped to the hydraulic classifier for classification, and the classifier underflow returned to the long cylindrical ball mill to form a closed circuit, while the classifier overflow was pumped to the vibrating tilted plate thickener.
Silicon powder dewatering : Process for silicon powder dewatering was thickening+ filtration. After the silicon powder was concentrated in the vibrating tilted plate thickener, the overflow water flowed to the return water sedimentation tank for precipitation, and the underflow flowed into the disc filter for filtration. The filtrate was pumped back to the vibrating tilted plate thickener by a submerged pump, while the filter cake was transported to the drying system by a belt conveyor.
The drying system adopted a tri tunnel rotary dryer with a dust removal system. The loose material was fed into the feeder sucked into the dryer by the high-temperature hot airflow for drying. The dried material entered the discharge system with the airflow, and then was discharged into the cooling system from the closed air discharger. The cooled dry materials entered the baler through the closed-air discharger for packaging, and the packaged finished products were sent to the finished product warehouse for sale.
Secondary fine powder dewatering : Process for silicon fine powder dewatering was thickening+ filtration. After being concentrated, the secondary fine powder overflow water flowed to the return water tank, and its underflow was pumped by the slurry pump to the filter press for filtration. The filtrate flowed to the return water tank, and the filter cake was transported by the belt conveyor to the secondary fine powder storage dump. Part of the thickener overflow was purified by pumping into the filter press, and the filtrate was pumped into another filter press for secondary purification. The filtrate after secondary purification was supplied to the water supply system of fine powder plant. The filter cake obtained by the two-stage purification was the solid slag, which was directly cleaned manually.
In the first phase of the project, the grade of fine silicon powder SiO2 was 99.95%; the grade of secondary silicon fine powder SiO2 was 97.55%; the yield of fine silicon powder was 69.92%; the yield of secondary silicon fine powder was 30.08; and the recovery rates of silicon powder and secondary silicon powder were 70.43% and 29.57, respectively. In the second phase of the project, the SiO2 grade of fine silicon powder was 99.99%; the yield of fine silicon powder was 95%; and the recovery rate of fine silicon powder was 95.04%.
To find out more about our products and solutions, please fill out the form below and one of our experts will get back to you shortly.