cases
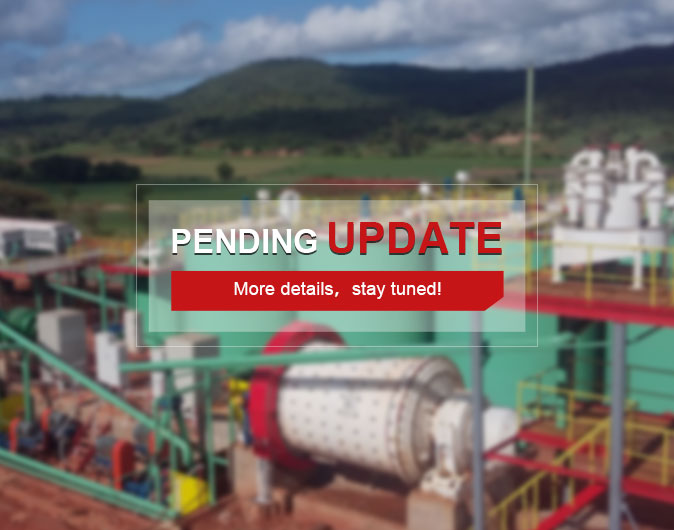
The main minerals were magnetite (60%-30%), followed by hematite and specularite (less than 3%). The content of pyrite was uneven, generally very small, up to 9% locally. The main composition of gangue was plagioclase (40%-70%), followed by a small amount of chlorite, epidote, carbonate, and occasionally chrysotile, sericite, dolomite, apatite, tourmaline and garnet.
Crushing and screening stage: After the raw ore was transported from the mining site to the raw ore storage yard of the processing plant by truck, the raw ore was pushed to the raw ore bin by a forklift, and then fed into the jaw crusher by the chute feeder for coarse crushing.The coarse crushing products were transported by a belt conveyor to an auto-centering vibrating screen for screening, and the products on the screen were returned to the jaw crusher through a belt for fine crushing. The fine products were also transported to the auto-centering vibrating screen for screening, forming a closed circuit. The products under the vibrating screen were transported to the powder ore bin for storage by a belt conveyor and the particle size of crushed products is - 15mm.
Grinding and classification stage: the powder ore was fed by the electric vibration feeder to the belt conveyor, which was evenly fed into the grid type ball mill for grinding, and was classified by the spiral classifier to form a closed circuit. The grinding fineness was -200 mesh, accounting for 65%.
Magnetic separation stage: the magnetic separation used a semi-counter current magnetic separator for one roughing and one cleaning to obtain magnetic separation concentrate. The tailings were scanned once by the magnetic separator, and the concentrate was pumped to the roughing magnetic separator for re-separation, and the scavenging tailings were used as the final tailings.
Dewatering stage of concentrate tailings: The dewatering of concentrate tailings adopted the two-stage dewatering process of concentration and filter press. The water content of final product was less than 15%, and dry tailings were used for brick making.
The TFe grade of the iron concentrate was 63%. The iron concentrate yield was 33.3%, and the iron recovery rate was 59.94%.
To find out more about our products and solutions, please fill out the form below and one of our experts will get back to you shortly.