cases
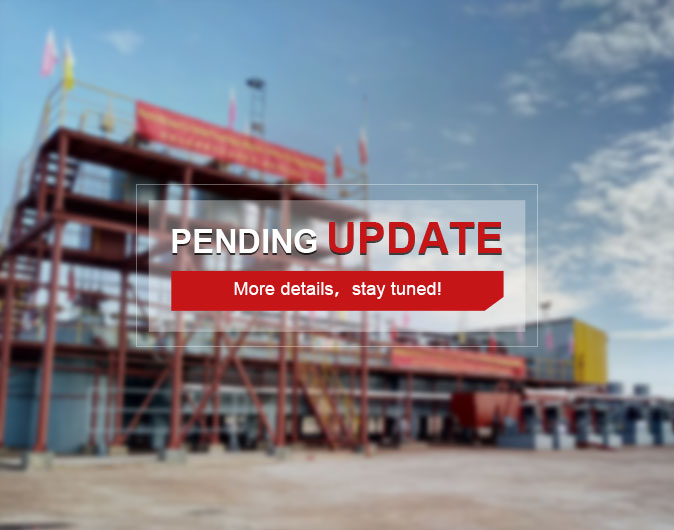
According to the oxidized degree, the ore was determined as semi-oxidized ore. According to mineral composition and textural & structure characteristics, the ore natural type was roughly divided as limonite siliceous breccias and limonite siliceous catalectic rock. Since the useful element in ore was gold, and the harmful elements were arsenic and antimony, the ore industrial type was determined as gold ore bearing arsenic and antimony.
Crushing and screening stage: The crushing particle size in this process was big, so phase two half closed-circuit process with compactness and practicability was adopted. The raw ore feed size was 350mm or less; phase two half closed-circuit process was adopted in crushing and screening; the final crushing size of product was -12mm.
Grinding and classification: Two-phase ore grinding was adopted for ore grinding. The grid ball mill was adopted for phase 1 ore grinding with fineness of -200 meshes, accounting for 65%; pumps and hydrocyclones were adopted for classification with hydrocyclones. The wet long-cylinder ball mill was adopted for phase 2 ore grinding with fineness of -325 meshes, accounting for 95%; pumps and hydrocyclones were adopted for classification with hydrocyclones.
Oxidation pre-treatment: The leaching tanks with double impellers were adopted for oxidation pre-treatment with oxidation pre-treatment duration of 60h. Slurry was dewatered by filter press after oxidation pre-treatment; dry ores entered the agitation tank for slurry-mixing, and filtrate from filter press entered sewage treatment system. Leaching and washing system: Mixed slurry entered the cyanide leaching system; cyanide leaching time was 48h; after phase 2 leaching and phase 3 washing, eventually the pregnant solution overflows from one-phase thickener. Zinc powder replacement system: Finally, the gold mud was obtained by purification, deoxidization and zinc powder replacement process of cyanided pregnant solution.
Tailings dewatering: Tailings dry stacking workshop was built on the northeast direction of the mineral processing plant for dewatering. Cyanided tailings entered the tailings dry stacking workshop; the free flow chamber filter press was adopted for the tailings dry stacking; the filter-pressed dry tailings were back washed again and again; final tailings were transported to the tailings pond for stacking by belt conveyor. Sewage treatment system: After pre-treatment, filtrate from filter press entered the thickening + filter-pressing two-phase sewage treatment system for abandoning trace impurity, and then it was conveyed by belt conveyor to the tailings pond for stacking. After treatment, water entered the backwater pond in pre-oxidation stage; backwater was recycled in the pre-oxidation stage.
For the stage 1 and 2, the gold leaching rate was 89.49%, the recovery rate was 88.01%.
To find out more about our products and solutions, please fill out the form below and one of our experts will get back to you shortly.