cases
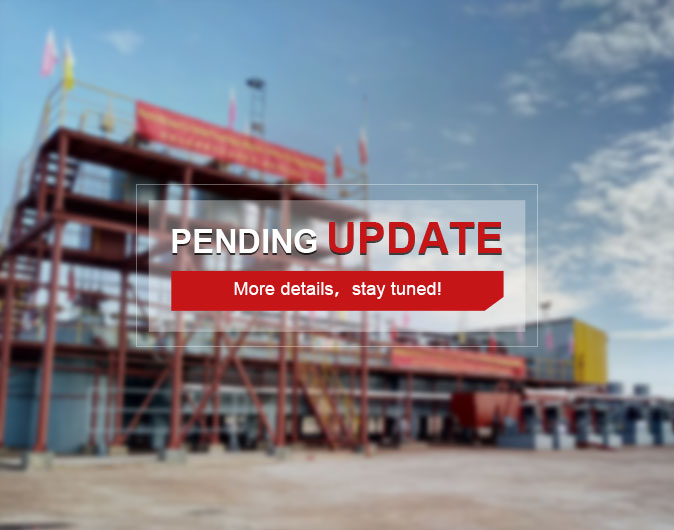
According to the site data provided by the client, Xinhai Mining EPC supplied this project with EPCM+O. The scope of design work contained: the gold ore heavy separation, the construction drawing design of cyanide mining processing plant (including tailings pond ), including the design of the production workshop of the processing plant, involving water supply and drainage, electricity, civil construction, general drawing and other specialties. The powder ore contained 0.26% copper, 3.1g/t gold, 43.41% iron and low content of other elements. The core ore contained 0.90 g/t gold, 25.45% iron, and low content of other elements. The gold was the mainly recovered elements.
The stage of crushing: The crushing process used one-stage open-circuit crushing. The ore was piled in the raw ore yard, and loaded with a forklift truck. A vibrating feeder was installed at the bottom of the primarybin which played the role of feeding and screening at the same time. The coarse ore was fed by a feeder to a jaw crusher for a stage of crushing, and the fine-grained ore and crushed ore were transported to the powder ore bin with a belt conveyor.
The stage of grinding and heavy separation:The grinding and grading operation of the first-stage project used a closed-circuit grinding and grading process. A feeder was installed at the bottom of the powder ore bin. The ore was sent to the belt conveyor by the belt feeder and then transported to the wet grid ball mill by the belt conveyor for grinding. The discharge of the ball mill entered the gravity separation process for one roughing and two concentration coarse- grained gravity separation. The concentrate from gravity separation was the coarse-grained concentrate, and tailings from gravity separation was pumped to the hydrocyclone fro grading.
The overflow from hydrocyclone flowed into the one roughing and two concentration fine-grained gravity separation. The concentrate from gravity separation was the fine-grained concentrate, and tailings from gravity separation was pumped to the tailings pond as the tailings of first-stage project.
The stage of cyanation:When processing raw ore, the overflow of the first stage of grading was pumped to the second stage of grading, and the overflow of the second stage of grading entered the cyanidation operation after chip removal. When processing tailings, the prepared tailings pulp was pumped to the second stage of grading, and the overflow of the second stage of grading entered the cyanidation operation. In order to facilitate the flow of the pulp, the height of the former leaching tank was higher than that of the next tank. The sodium cyanide reagent was delivered to several leaching tanks by a magnetic pump, and a Roots blower blowed air into each leaching tank. New activated carbon was added to the last leaching tank. At intervals, the gold in the latter leaching tank was lifted by the airlift and sent to the previous leaching tank, and so on, until to the first leaching tank. After the gold-loaded carbon was lifted out of the first leaching tank, and separated by the carbon extraction screen, the pulp return was returned to the first leaching tank. A cylindrical carbon screen was installed at the outlet of each leaching tank to prevent the activated carbon from flowing into the next leaching tank.
The stage of desorption electrolysis:The gold-loaded carbon was sent to the desorption electrolysis workshop to produce gold mud. This desorption electrolysis system was a complete set of equipment and automatically controlled in advance. With the working temperature of 150° and the working pressure of about 0.5 MPa, this desorption electrolysis system had high working efficiency and only 12-15 hours working time. The system used sodium hydroxide instead of sodium cyanide because of the low cost. The complete system included gold-loaded carbon storage tank, desorption column, heater, filter, electrolysis tank, desorption solution preparation tank, pipeline, valve, instrument, pump, air compressor, electric control cabinet, rectifier cabinet, etc. The gold mud produced by electrolysis could be smelted by an intermediate frequency furnace after pickling and other processing to obtain gold bars.
The stage of carbon regeneration:After desorption and electrolysis, the lean carbon entered the carbon regeneration system, where the lean carbon was first regenerated by pickling in the pickling tank, and the pickling liquid was adjusted to neutral in the neutralization tank and discharged by the submerged pump. The regenerated activated carbon is returned to the cyanide leaching system of the processing plant to realize the reuse of activated carbon. The activated carbon was regenerated by the pickling once for each desorption, and after 3 to 5 times, it was regenerated by high temperature.
Tailings dehydration system:After the leaching, tailings were separated from the fine-grained charcoal in the pulp through a safety screen and entered to the filter press for filter press dehydration. The water content of the filter cake after dehydration was 10%-20%.
The core is ground to 85% of -200 mesh. Lime was used as protective alkali, sodium cyanide dosage was 1.5kg/t, leaching time was 16h, and gold leaching rate was 80.00%.
To find out more about our products and solutions, please fill out the form below and one of our experts will get back to you shortly.