cases
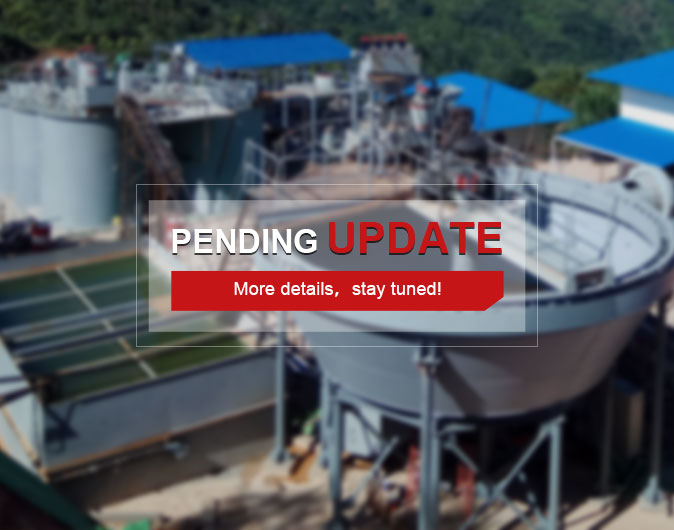
The scale of project was 1200t/d, with main processed products of silver concentrate and manganese concentrate.
Crushing and screening stage: In the crushing andscreening stage, adopted three stage and one closed circuit crushing andscreening flow. Using jaw crusher for coarse particles and cone crusher formedium and fine particles, the crushed particles’ size was -12mm;
Grinding and classification stage: The grinding process adopted two stage fully closed circuit grinding, and the grinding operation wasdivided into two series. The first stage grinding used grid ball mill and spiral classifier to form a closed circuit grinding, and the second utilized overflow ball mill and high-efficiency cyclone group to form a closed circuit grinding, with a grinding fineness of -200 mesh accounting for 85%;
SO2 manganese leaching stage: the qualified product of grinding and SO2 treated by high temperature entered together the cooling towerfor cooling and mixing. After mixing, the slurry entered double impeller leaching tank for continuous manganese leaching. With manganese leaching done,it was pumped into the thickener for continuous three-stage washing. The overflow from the second and third washing stage was returned back to washing operation in previous stage. The overflow of washing operation from the firststage was the precious manganese sulfate liquid, which flowed into manganese sulfate storage tank, finally obtaining manganese sulfate crystals; the slurry after the third washing stage entered silver leaching stage; Silver leaching stage: After washed in manganese leaching stage, the slurry entered the agitation tank, adding milk of lime for adjustment,then pumped it into double impeller leaching tank to continue adding the milkof lime to adjust slurry. After adjustment operation, let it enter double impeller leaching tank for leaching. The slurry was pumped into thickener to perform acontinuous three-stage washing operation. The overflow from the second and third stage was returned to washing operation in the previous stage. The overflow from washing operation in first stage was the silver-containing precious liquid, which flowed into precious liquid pool by itself; The silver-containing precious liquid was pumped intoplate and frame filter press for first stage purification and filtration, and then pumped into the plate and frame filter press for the second stage purification and filtration. The filter cakes of two stage purification andfiltration were pumped in rubber belt filter press for filtration. The filtrate and two-stage purified silver-containing precious liquid were all pumped intodeoxidation tower for deoxidation, and then pumped into plate and frame filter press by pump added with zinc powder in order to obtain silver mud, which could be sent to smelting workshop for smelting; the replaced solution was considered as lean liquid, which flowed into lean liquid pool by itself, and then could beused as return water to the washing stage;
Tailings treatment stage: Pumped into double impellerleaching agitation tank, the washed pulp in the silver leaching stage was cyanide-containingtailings. Cyanide-containing tailings and filter cake from belt filter press wereadded together with bleaching powder for neutralization, and then were pumped intailings pond.
In implementation of the project, aimed at improving labor productivity and economic benefit, Xinhai adopted new equipment and new technology as much as possible. On the basis of existing conditions, it made full use of topographical conditions to build factories and save enterprise investment.
To find out more about our products and solutions, please fill out the form below and one of our experts will get back to you shortly.