cases
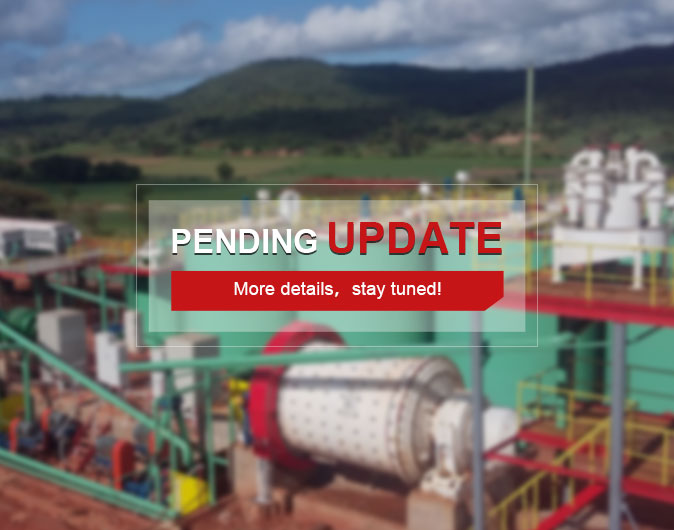
Xinhai designed the process of two stage one closed circuit crushing screening - three stage closed circuit grinding - flotation - concentrate dehydration for Inner Mongolia Chifeng 2000TPD Molybdenum concentrator.The project is a whole industry Chain service (EPCM+O) project of mining industry.
Crushing and screening stage: Two-stage one closed-circuit crushing and screening process was adopted. The raw ore was stored in the raw ore yard, and the ore was loaded with a forklift. The rod feeder at the bottom of the raw ore bin had both feeding and screening functions. The screened material was fed into the Nordberg crusher for coarse crushing, and then transported to the circular vibrating screen by the 1# belt conveyor. After the material on the screen entered the buffer bin directly, it was fed into the belt conveyor by the motor vibrating feeder and transported to the Nordberg crusher for fine crushing. The finely crushed products and the coarsely crushed products were returned to the vibrating screen together to form closed-circuit crushing. The material under the screen (-15mm) was the qualified material in the crushing stage and directly entered the powder ore bin.
Grinding stage: The three stage closed-circuit grinding + flotation (one roughing, two scavenging and seven cleaning + two fine scavenging) process was adopted. An electric vibrating feeder was installed at the bottom of the powder ore bin, which was transported to the overflow ball mill for coarse grinding by a belt conveyor. The discharge of the ball mill was pumped into the hydrocyclone group for one stage classification, then the underflow of one stage classification was returned to the ball mill for further grinding, forming the first stage closed-circuit grinding process. The overflow of one stage classification flowed into a pump box, and was pumped into the second classification stage of the hydrocyclone group by the pump. The underflow flowed into another overflow ball mill for the second stage grinding, and the discharge flowed into the above pump box by itself. Together with the overflow of one stage classification, the discharge was pumped into the second stage of classification to form the second stage closed-circuit grinding process, with a grinding fineness of -200 mesh accounting for 80%.
Separation stage: The overflow of second-stage grinding flowed into the high-efficiency agitating tank after dosing and mixing, and then flowed to the 8m³air-inflation flotation machine for rough separation. The rough froth product flowed to the SF-2.8 flotation machine for cleaning I and the products after cleaning I flowed into the SF-2.8 flotation machine for two stages of fine scavenging (2/2). The foam products of fine scavenging I and II were returned to the upper garment in turn, and the tailings of fine scavenging II were the final tailings. The product in the roughing tank flowed to two scavenging operations. The flotation machines used in two scavenging were 8m³ air- inflation flotation machines. The first scavenging and second scavenging foam products were returned to the previous operation in turn. The scavenging II tailings were also the final flotation tailings. Together with the fine scavenging II tailings, it was pumped to the tailings pond. The foam product of cleaning I flowed into a pump box, and the pump was driven into the hydrocyclone for three-stage classification. The underflow flowed into the cone ball mill for regrind, and the discharge flowed into the above pump box, together with the foam product of cleaning I to enter the three stages of grinding driven by the pump to form the third stage closed-circuit grinding process, with a grinding fineness of -400 mesh accounting for 88%. The overflow of the three-stage grinding flowed into the high-efficiency reformed thickener, and the overflow can be used as backwater to return to the system for reuse; the bottom flow flowed into the high-efficiency agitation tank and then flowed to 10 (3/2/2/1/1) /1) sets of SF-0.37 flotation machine to carry out cleaning II-VII. Then the products in the cleaning III-VII tanks returned to the previous operation in turn, and the products in the cleaning II tank return to the cleaning I. At last, the foam product of the cleaning VII was molybdenum concentrate.
Concentrate dehydration stage: the molybdenum concentrate was dehydrated by mechanical dehydration. The molybdenum concentrate was pumped into the high-efficiency reformed thickener, and the underflow was pumped into the chamber filter press. Then the filter cake was transported by the belt conveyor to the dryer for drying and then stored in the concentrate bin. The filtrate was pumped into the tailings pond; the thickener overflow can be used as backwater to return to the system for reuse.
To find out more about our products and solutions, please fill out the form below and one of our experts will get back to you shortly.