cases
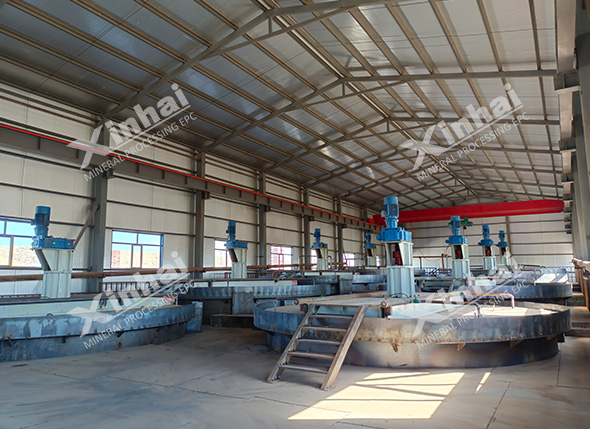
The main gold-bearing mineral in the ores was electrum, and the silver-bearing minerals were argentite, natural silver, sulfide, pearceite and electrum. The main metallic minerals were pyrite, sphalerite and galena, a small amount of chalcopyrite, chalcocite and arsenopyrite. The metal oxides were mainly magnetite, hematite, siderite, chromite, psilomelane, etc. Only contents of magnetite and hematite were up to 0.89%. the gangue minerals were mainly quartz, sanidine, plagioclase and a small amount of flaky mica (mainly white mica and sericite).
Crushing: The crushing system used the original four-stage incomplete closed-circuit crushing process, and the particle size of crushing product was 12-0mm.
Grinding + flotation: Two-stage continuous grinding, one time of open-circuit roughing + roughing, two times of scavenging, one time of concentration process. The flotation tailings were sent to the tailings dry stacking system, rapid flotation concentrate combined with the flotation concentrate and then entered to concentrate grinding, leaching zinc powder displacement system. Dewatering and regrinding of comprehensive concentrate: The concentrate of one-stage flotation and two-stage flotation were fed into the concentrate regrinding operation. Since the flotation system and the comprehensive concentrate leaching system adopted the stage backwater, the comprehensive flotation concentrate adopted two-stage mechanical dewatering process. After mixing the filter cake, a closed-circuit grinding composed of overflow ball mill and cyclone was used for re-grinding. The grinding fineness was -0.041mm (90%).
Comprehensive concentrate leaching, displacement and tailings dewatering: For the leaching concentration, the thickener overflow was gold and silver-bearing precious liquid, which flew to the liquid storage tank. The suspended solid of gold-bearing precious liquid was less than 5ppm via purification and filtration, the filtrate flew to the precious liquid tank, then was absorbed to the deoxygenation tower through vacuum system. The zinc powder was fed into the zinc powder displacement, then the gold mud was obtained by the displacement filter press. The gold mud was the middling product with 30% of silver, which was sent to the smelting workshop. The displaced filtrate flew to the lean liquid displacement tank for pulp mixing and washing. The leaching slag entered to the press filter after washing, the filter cake entered to the backwater system after washing. Cyanide removal and flotation of cyanide residue: There were some recoverable lead and zinc in the raw ore, which can be enriched to a certain grade after the silver flotation process. The washed cyanide residue contained CN-10mg/L and was enriched in the tailings through the cyanide leaching and washing. In order to comprehensively recover lead and zinc from cyanide residue, the flotation of lead and zinc from leaching residue was carried out. The lead flotation adopted one-stage roughing, one-stage scavenging, three-stage concentration to extract the lead concentrate. The lead flotation tailings were sent to the zinc flotation operation. The zinc flotation operation adopted one-stage roughing, two-stage scavenging, three-stage concentration to extract the zinc concentrate. Then, the zinc flotation tailings and silver flotation tailings were sent to the tailings dewatering operation, and discharged after reaching the standard.
Lead and zinc concentrate dewatering: The dewatering of lead concentrate and zinc concentrate adopted two-stage mechanized dewatering operation. The thickener was used for the first stage concentration, and the ceramic vacuum filter was used for the second stage dewatering. After filtration, the filter cake was the final lead concentrate and zinc concentrate, which were discharged to the concentrate tank for sale. Tailings dewatering: The flotation tailings were pumped to the slurry buffer tank in the tailings dry stacking workshop, and then pumped to the dewatering cyclone for dewatering and classification. The underflow of the cyclone entered the dewatering screen for two-stage dewatering. The undersize dry material of the dewatering screen contained about 20% water and was transported to the tailings pond for dry storage through the belt conveyor. The undersize of dewatering screen entered into the tailings buffer tank, and the cyclone overflow entered the thickener for concentration and dewatering. After dewatering, the thickener underflow was dewatered by the press filter. The water content of the filter press tailings was about 20%, and the dewatered dry tailings were transported to the tailings pond for storage. The overflow water of the thickener and the filter press returned to the water recycling tank for recycling. Backwater system: The backwater system was divided into flotation backwater recycling system and the cyanide backwater recycling system.
For the ore in I area and outsourcing ore, the grade of Ag concentrate was 972.46g/t, and the total recovery rate was 78.31%. For the ore in II area, the grade of Ag concentrate was 1472.88g /t, the total recovery was 80.15%, and the total recovery rate of Au was 90.32%.
To find out more about our products and solutions, please fill out the form below and one of our experts will get back to you shortly.