cases
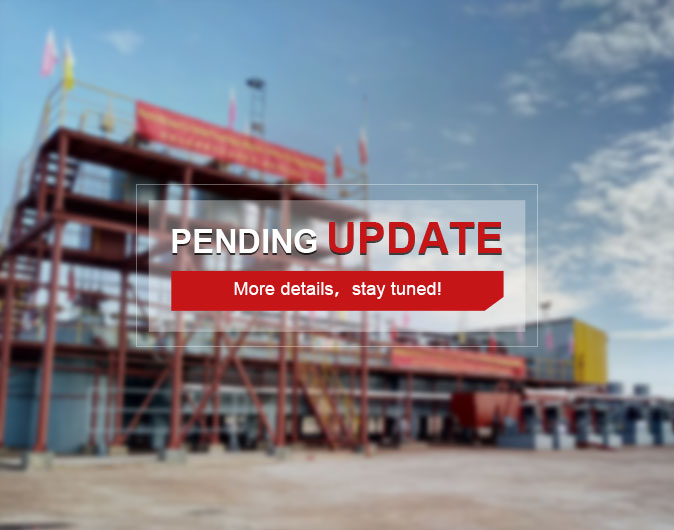
Chongli 300t/d gold mineral processing plant is an EPCM+O project undertaken by Xinhai, which is solely undertaken by Xinhai from design and research, manufacturing and procurement of complete sets of equipment, commissioning and delivery to mine management and operation.
Two-stage one closed-circuitcrushing and screening process was adopted.
First, the raw ore was fedinto the ground raw ore bin, and then fed to the jaw crusher by the chutefeeder for coarse crushing. Then, the crushed ore was transported by the 1#belt conveyor to the circular vibrating screen for screening. The products on theupper sieve and the intermediate products of the sieve were combined and fedinto the cone crusher for fine crushing by the 2# belt conveyor. After the finecrushing, the products are combined and fed to the 1# belt conveyor and thenreturned to the sieve for screening. The final product under the sieve wastransported by the 3# belt conveyor to the powder ore bin for storage, forminga second stage and one closed-circuit crushing and screening process. And thefinal crushing size was -20mm.
Grindingand beneficiation stage: a process of closed-circuit grinding + gravity separation + flotation(one roughing, two scavenging and two concentration) was adopted.
The material in the fine orebin was fed to the 4# belt conveyor by the electric vibration feeder, and was transportedto the wet grid type ball mill for grinding. The discharge of the ball millflowed through the built-in cylindrical screen to remove large particles(larger than 4mm), the slurry under thescreen entered the pump box, the slurry pump is pumped to the cyclone group forclassification. The slurry under the screen entered the pump box first, andthen was pumped by the slurry pump to the cyclone for classification, andthe sand setting of the cyclone was returnedto the ball mill for regrind.
The overflow of the cycloneflowed into the high-efficiency stirring tank for adding chemical and stirring.After mixing, the slurry was fed into the flotation machine for one roughing,two scavenging and two concentration flotation operations. XCF/KYF-4 flotationunit was used for roughing, SF-1.2 flotation unit was used for concentration,and XCF/KYF-4 flotation unit was used for scavenging.
The tailings flowed intothe tailings pond.
Concentratedehydration stage: the flotation gold concentrate was dewatered by thickener + filter press.
The gold concentrate fromthe flotation flowed to the high-efficiency thickener for a stage ofdehydration. Then, the underflow of the thickener was pumped to the box filterpress with a wear-resistant two-stage pump for dehydration. The concentrateentered the concentrate storage yard, and the filtrate flowed to the thickener.
To find out more about our products and solutions, please fill out the form below and one of our experts will get back to you shortly.