cases
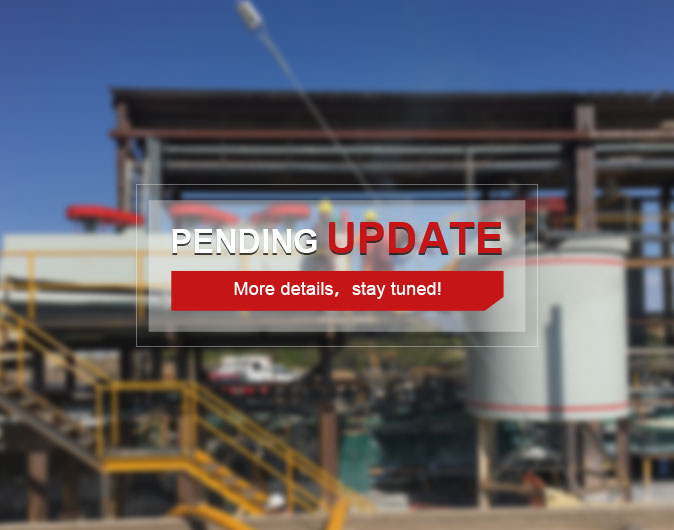
Inner Mongolia 1200tpd lead-zinc processing plant is a mining industry chain service (EPCM+O) project undertaken by Xinhai, which is solely undertaken by Xinhai from design and research, manufacturing and procurement of complete sets of equipment, commissioning and delivery to mine management and operation.
Crushing and screening stage: Two and half stage closed-circuit crushing and screening process was adopted. The raw materials were stored in the raw ore bin, equipping with the electric vibration feeder at the bottom. Materials were fed to jaw crusher for coarse crushing. Crushed materials were transported by 1# belt conveyor to the double circular vibrating screen. Oversized materials were transported to the crusher for middle crushing; middle crushing and screening materials were transported by 2# belt conveyor to the Nordberg crusher for fine crushing; fine and rough crushing materials returned to the vibrating screen forming closed-circuit crushing. Oversized materials were sent to the fine ore bin by 3# belt conveyor.
Grinding stage: Three stage closed-circuit grinding, lead flotation, zinc flotation, and sulfur flotation process was adopted. The bottom of the fine ore bin was equipped with the pendulum feeder. Fine ore was sent to the straight-cylinder ball mill for rough grinding by the 4# belt conveyor. Grinding materials were pumped into hydrocyclone for classifying, and underflow returned to the ball mill, which formed the first stage closed-circuit grinding.
Concentration stage: The overflow flowed to the lifting agitation tank and then entered the lead-zinc flotation roughing. Roughing tailings sequentially entered two stage scavenging. Scavenging II concentrate returned to scavenging I; scavenging I concentrate returned to roughing; scavenging II tailings were lead-zinc flotation separation tailings. The roughing concentrate flowing into the pump box was pumped into the hydrocyclone for classification, with underflow entering the cone ball mill for fine grinding. Grinding material entered the mentioned pump and returned to the mill with the roughing concentrate to form the second closed-circuit grinding. After hydrocyclone overflow was lifted to the agitation tank, it entered four-stage lead concentration in sequence. Concentration IV tailings returned to concentration III; concentration III tailings returned to concentration II; concentration II tailings returned to concentration I; concentration I tailings returned to roughing. Finally, the closed-circuit flotation with one stage roughing, two stage scavenging, and four stage concentration was formed. Lead-zinc flotation tailings flowed to the lifting agitation tank and then entered zinc roughing. Roughing tailings sequentially entered three stage scavenging. Scavenging III concentrate returned to scavenging II, scavenging II concentrate returned to scavenging I, and scavenging I concentrate returned to roughing. Scavenging III tailings were zinc flotation tailings. The roughing concentrate flowing into the pump box was pumped into the hydrocyclone for classification, with underflow entering the cone ball mill for fine grinding. Grinding material entered the mentioned pump box and returned to the mill with the roughing concentrate to form the third closed-circuit grinding. After hydrocyclone overflow was lifted to the agitation tank, it entered four-stage zinc concentration in sequence. Concentration IV tailings returned to concentration III; concentration III tailings returned to concentration II; concentration II tailings returned to concentration I; concentration I tailings returned to roughing. Finally, the closed-circuit zinc flotation with one-stage roughing, three-stage scavenging, and four-stage concentration was formed. Zinc flotation tailings flowed into the lifting agitation tank and were lifted to sulfur roughing. Roughing concentrate was concentrated and pumped by settling pond for dewatering;concentration tailings returned to the roughing process. Roughing tailings entered the scavenging process, and scavenging concentrate returned to the roughing process, forming closed-circuit sulfur flotation of one stage roughing, one stage scavenging, and one stage concentration. Scavenging tailings were pumped to the tailings pond.
Concentrate dewatering stage: Small amount of sulfide concentrate was pumped to the settling pond for dewatering; lead-zinc concentrate was dewatered mechanically. Flotation lead concentrate was pumped into the central driving thickener; underflow entered into ordinary agitation tank and was pumped into the high-pressure press filter for filtration; filter cake was transported by the belt conveyor to the concentrating pond. Flotation zinc concentrate was pumped into the efficient improved thickener; underflow entered into the ordinary agitation tank and was pumped into the high-pressure press filter for filtration; filter cake was transported by the belt conveyor to the concentrating pond. The overflow and filtrate in the dewatering process returned for recycling.
To find out more about our products and solutions, please fill out the form below and one of our experts will get back to you shortly.