cases
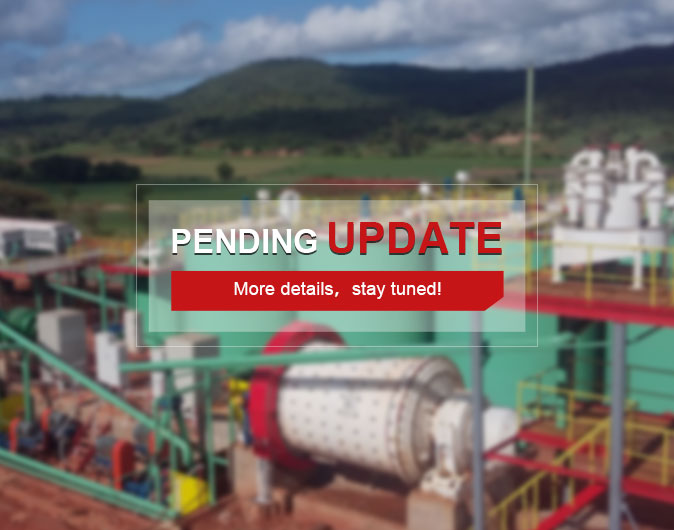
This project was divided into two phases, the first phase was 2000 t/d, and the second phase was expanded to 3000 t/d. In the first phase of the design, the second phase was also taken into account. In order to save investment and shorten the construction period, the main equipment of the crushing system was directly considered according to the production capacity of 3000 t/d. The grinding, flotation and dehydration equipment had some surplus to meet the production scale of Phase I. So in the second phase, the production scale of 3000 t/d could be reached only by adding or replacing part of the equipment.
The stage of crushing and screening: Use two-and-half-stage and one closed-circuit process, the final particle size of the crushed product was 12 mm.
Grinding and grading stage: First stage used a grid ball mill to grind and a pump + hydrocyclone to grade; Second stage was to re-grind the coarse concentrate of lead with a overflow tube ball mill for grinding and a pump + hydrocyclone for grading.
The stage of flotation: In order to ensure the recovery rate and the quality of lead and zinc concentrates, a zinc concentration was added on the basis of the recommended process of the mineral processing test, and a lead and zinc scavenging were added respectively. The process of flotation was composed of selecting lead first, then zinc from lead tailings. It used the process flow of one-roughing, three-scavenging and three-concentration to select the lead, firstly lead tailings and then zinc selection; it used the process flow of one-roughing, three-scavenging and four-concentration to select the zinc. All of flotation cells are air-charging flotation cells, the unit of XCF/KYF-16 flotation cell for the scavenging of lead and zinc, and the unit of XCF/KYF-8 flotation cell for the concentration.
The dehydration stage of lead and zinc concentrates: Use two-stage mechanized dehydration process. First stage, it used the high-efficiency modified thickener to dehydrate lead and zinc concentrates; Second stage, it used the membrane filter press to filter and dehydrate the lead concentrate. The zinc concentrate was filtered and dehydrated by the ceramic-medium filter. After dehydration, the water content of the lead and zinc concentrate was less than 12%.
The dehydration stage of tailings: At the end of the processing plant, tailings were discarded in a wet manner. The final tailings from the processing plant were transported to the tailings pond with a plunger pump for precipitation. Tailings were deposited in the pond, and the clarified water was pumped back to the production pond of the plant for recycling, thereby realizing zero discharge of wastewater during the the plant's production.
In the first phase of this project, the grade of lead concentrate was 69.02%, zinc concentrate was 51.02%, the productivity of lead concentrate was 2.88%, zinc concentrate was 4.71%, the recovery rate of lead concentrate was 90.00%, the recovery rate of zinc concentrate was 89.00%. In the second phase, the grade of raw ore declined. But the property of raw ore remained the same, the recovery rate and the grade of the concentrate remain the same except that the production of lead, zinc concentrate and silver decreased from year to year.
To find out more about our products and solutions, please fill out the form below and one of our experts will get back to you shortly.