cases
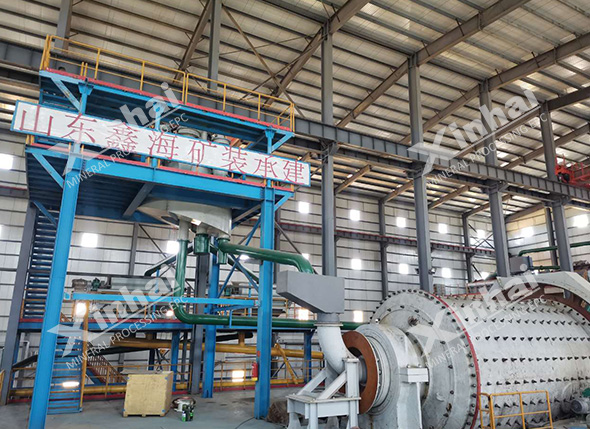
The metallic minerals were magnetite, hematite, limonite; the non-metallic mineral was quartz. Only Fe in the raw ores has recycling value, and the raw ores belong to original acid magnetite with low phosphorus and low sulphur.
Crushing and screening stage: The process of three-stage crushing and screening with single closed-circuit stage was adopted. The particle size of final crushing products was -15mm. Before the final crushing products were transported into fine ore bin, tailings discarding was conducted by magnetic pulley to discard non-magnetic waste rocks. The waste rocks were classified into two size fractions of 0-8mm and 8-15mm for sale.
Grinding and magnetic separation stage: The process of stage-grinding and stage-separation was adopted. The mills of first-stage, second-stage and third-stage grinding were respectively grid ball mill, overflow ball mill, and overflow ball mill, three mills in total; the grinding fineness of them was respectively -200 meshes (40%), -200 meshes (87%), and -325 meshes (95%). The magnetic field intensities of magnetic separators used in the first-stage, second-stage and third-stage magnetic separation were respectively 4,000Oe, 4,000Oe, and 1,000Oe.
Concentrates dewatering stage: Magnetic concentrates were dewatered preliminarily by concentrated magnetic separator. After dewatering, iron concentrates were further dewatered by disc vacuum filter. The first-grade iron concentrates (grade: >65%) were dewatered by disc vacuum filter, while the second-stage iron concentrates (grade: 50~60%) were dewatered by disc vacuum filter.
Tailings dewatering stage: The tailings were firstly processed by thickeners for the first-stage dewatering; after that, the underflow was transported by the slurry pump to hydrocyclone for classification. The settling of hydrocyclone flows by gravity into dewatering screen for dewatering, while the overflow flows by gravity into the updated high-efficiency thickener for second-stage thickening. The underflow of the second-stage thickener was transported by the slurry pump to press filter for dewatering. The overflow water of the first-stage and second-stage thickeners were collected into backwater pond for cyclic utilization.
The grade of first-stage iron concentrates was 65.06%, the yield of first-stage iron concentrates was 31.00%, the recovery of first-grade iron concentrates was 54.75%; the grade of second-stage iron concentrates was 51.95%, the yield of second-stage iron concentrates was 5.00%, the recovery of second-grade iron concentrates was 7.05%.
To find out more about our products and solutions, please fill out the form below and one of our experts will get back to you shortly.