cases
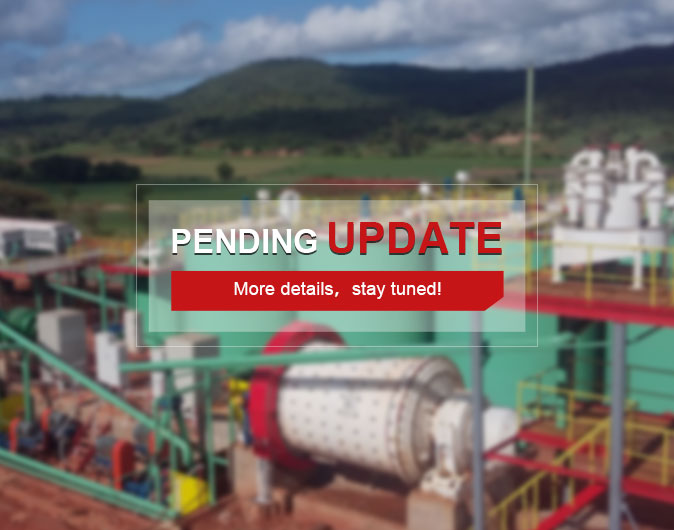
The metallic minerals of the project were mainly wolframite, pyrite, limonite, sphalerite, and chalcopyrite; the non-metallic minerals were mainly quartz.
The stage of crushing and screening: The feed size of the ore was ≤350mm, and the final crushed product size was -20mm.
The stage of grinding and grading: It used the one-stage grinding by a wet rod mill with the grinding fineness of -32 mesh, accounting for 100%. The discharge port used a linear screen to screen out large pieces which were returned to the rod mill with a belt conveyor for regrinding. The high-frequency vibrating screen was used for grading.
Desliming gravity separation: The qualified products of grinding were deslimed and graded by a segmented continuous hydroclassifier. The pulp of different grain sizes entered the spiral chute for roughing gravity separation. The selected heavy sand was concentrated by a shaking table, and the gravity separation concentrate was finally selected.
Magnetic separation: Concentrate selected by shaking table of gravity separation underwent a section of medium-field-strength magnetic separation and a section of high-field-strength magnetic separation to remove impurities for selecting first-grade wolfram concentrate. The slime from the hydroclassifier and the tailings of the +200 mesh -120 mesh from spiral chute entered the secondary tungsten concentrate magnetic separation operation. The secondary tungsten concentrate products were selected after a period of medium-field-strength magnetic separation and a period of high-field-strength magnetic separation.
The stage of tailings dehydration: The tailings were divided into fine mud tailings and coarse sand tailings. The fine mud tailings were dehydrated by a thickener once, and the underflow of the thickener was dehydrated twice by a filter press. The coarse sand tailings were concentrated and graded by a cyclone, and the underflow of the cyclone was dehydrated with a dewatering screen for secondary dehydration. The overflow of the cyclone flowed to the fine mud tailings thickener for dehydration together with the fine mud tailings. The underflow of the dewatering screen was pumped into the fine mud tailings thickener and dehydrated together with the fine mud tailings by a submerged pump. The overflow of the thickener was returned to the production water recycling tank for recycling.
The grade of first class tungsten concentrates was 65.3%, the yield was 0.88%, and the recovery rate was 72.74%. The grade of the secondary tungsten concentrate was 15.3%, the yield was 0.26%, and the recovery rate was 5.03%.
To find out more about our products and solutions, please fill out the form below and one of our experts will get back to you shortly.